Completed Projects
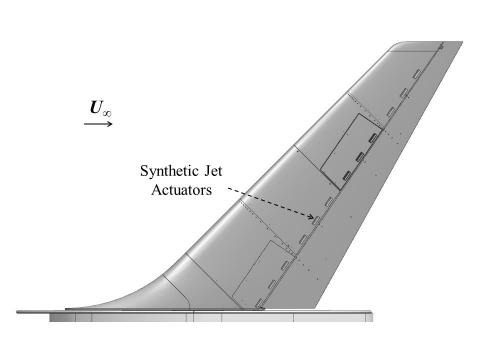
The addition of active flow control devices, such as synthetic jet actuators, on three-dimensional aerodynamic surfaces (i.e. vertical tail, wings, etc.) can lead to significant flowfield modification for beneficial improvements in aerodyanmic performance. Previous work by Dr. Nicholas Rathay and collaborators on this project focused on augmenting the side force generated by synthetic jets through separation control on scaled vertical tail models. Since commercial airplane tails are sized based on a single engine failure situation, they are larger than necessary for normal flight.
This project is acutely focused on the fundamental fluid physics governing the unsteady loads experienced by non-streamlined objects. Bluff bodies, as they are commonly known, experience abrupt separation of the flow which subjects them to the consequences of flows which may be unsteady and in many cases, transitioning from laminar towards turbulence. Examples of bluff bodies include tall buildings, bridge decks, and slung-load containers. One archetype geometry which has proven itself to be a benchmark for other studies is the rectangular prism.
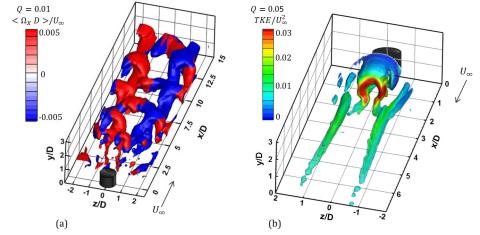
In general, the behavior in the wake of a wall-mounted circular cylinder with finite height is considerably different from that of two-dimensional bluff bodies. Unlike the flow field associated with a conventional 2D cylinder, a cantilevered finite-span cylinder is largely influenced by the presence of a spanwise (i.e., along the height of the cylinder) velocity component, most notably the downwash issued from the free end of the cylinder.

This project investigates the use of active flow control on square bluff bodies relevant to tall buildings. The research seeks to ameliorate the unsteady loading by controlling the formation and development of the von-Kármán vortex street, which is known to be the cause of undesirable building motion. More specifically, a fluidic jet is periodically excited at each of leading edges of a square prism where the shear layers separate and evolve into the large-scale vortex shedding in the wake.
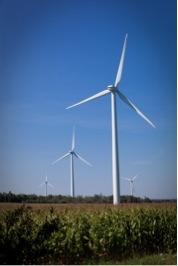
Recent developments in flow control techniques, coupled with increased interest in green energy technologies, have led to interest in applying flow control techniques to wind turbines, in an effort to reduce structural stress associated with widely varying loading.
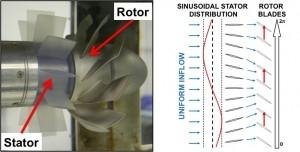
Developing a single propulsion and control concept for UUV’s that can provide more degrees of freedom and better control effectiveness compared with current technologies.